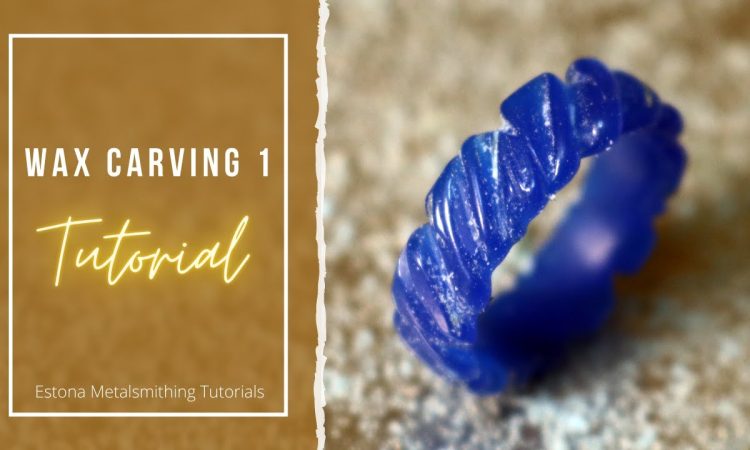
Casting is a kind of metal processing technology that human beings have mastered relatively early, with a history of about 6,000 years. The casting method used to make jewelry is different from that used to make sculpture. We first get the model by carving a wax mold or making a rubber mold, and then fuse the wax model to the wax column to make a “wax tree”. Next, the sculptor would put the metal bucket over the “wax tree,” mix some gypsum, and pour it into it. After the plaster is hardened, the wax model is melted away and discharged. Then the liquid metal liquid is injected by centrifugal casting or vacuum casting. Finally, the plaster is blasted to remove the object.
Similarly, wax carving techniques have a long history. Thousands of years ago, people used natural wax materials as jewelry production materials, combined with metal smelting and casting technology to produce a large number of exquisite jewelry. The wax carving technique has been developed so far, and it is favored by jewelry students and designers because of its vivid shape and simple operation.
In addition to the use of gold and silver hand-carved jewelry, the wax carving process is also one of the essential skills in DIY jewelry. This is also one of the best ways to understand the overall structure of the process of making jewelry.
For you to learn the most basic techniques of wax carving and master good technical essentials, I will give you a focus on the various tools required for wax carving. I will also focus on the characteristics and use of different properties of wax materials.
The main type of wax for jewelry
The wax used in jewelry carving wax is made of special component wax, which is divided into three categories according to hardness: hard wax, soft wax, and casting wax.
The first is hard wax, also known as carving wax. Hard wax has enough hardness, so we can use a variety of tools to carve, cut, file, drill, and so on. The quality of hard wax is hard but not brittle and is most commonly used for carving candles. Hard wax should be segmented by a professional wax saw blade. It’s less likely to get stuck than a regular saw blade. Hard wax is further divided into:
1) Flake wax: It is used to carve brooches and pendants.
2) Hole tubular wax: It is used to carve rings.
3) Wax core: It is used to inlay wax claws of various specifications, models, and shapes.
The second is soft wax. Because of its soft nature, we can bend it directly by hand or use thread wax to make shapes. I am used to fabricating it directly into a natural and vivid curve, which can inspire designers. In the United States, Ferris brand sculpting wax, for example, green hardness is the highest, purple hardness is moderate, and blue hardness is the lowest. Different colors of wax are based on a company’s research or production habits, there is no specific standard. Soft wax is divided into:
1) Flake wax: It comes in different thicknesses. Each thickness has its purpose.
2) Linear wax: It is used to decorate edges and plant stems and veins.
3) Spare wax: It is a soft wax in the shape of clay. I mainly use it to finish the corner repair work.
Tools for carving wax
First, you need to have a workbench. If you do not have a metalworking table, ordinary tables can also be used for early simple operations. It is obvious how easy and convenient it is to carve jewelry with wax. However, I still recommend that you perform the following operation exercises on a solid wooden jewelry workbench. Because the professional workbench is more suitable for placing tools and installing the crane, as well as collecting the powder cut down, and so on.
The tools used for carving wax mainly include carving wax knives, pneumatic engravers, cranes and various grinding needles, wax files, brushes, machine scissors, internal calipers, and other tools.
In short, after the wax mold is cast, you can polish the details of the jewelry with the metalworking process, and a complete piece of jewelry is born.
Types of cutting tools
So next, I will first give you the most common configuration of science – knives.
The knife is one of the most important tools in wax carving, and the knife method is mainly cutting and scraping. What are the commonly used carving knives? I have summarized the following for you. First, there are ordinary carving knives, such as woodcut knives, seal cutting knives, pottery knives and so on, which can be easily bought in art supply shops. The second is the more advanced professional knives, generally sold in a set, its price is more expensive. The tools suitable for scraping are mainly knives with relatively thin blades, mainly scalpels and ring wax knives.
The scalpel is composed of a handle and a blade. Commonly used blades are No. 10, No. 11 and No. 12 three types. Because the wax material is extremely delicate, the surface of the work is often treated by scraping in the process of wax carving to make it smooth and smooth. The method of scraping is easy to master, that is, the blade is inclined to the wax surface about 45° for the same direction scraping. The tip of the scalpel is very sharp and sharp, and many details and angles can be carved with the tip of the knife, as well as the work of drawing lines on the draft.
A ring wax knife is a special tool to enlarge the size of wax rings. It is marked with a hand-inch scale and has a blade on the side. It mainly uses rotary planning to expand the inner ring. However, it is worth noting that because it is a narrow shape, the positive and negative sides of the ring need to be shaved separately during the planning process. This will ensure that the inner ring is the same thickness.
Wax file and sandpaper
A wax file and repair tool specially used for wax carving. It is mainly used to trim the wax mold to various angles and radians and highlight the shape of the work. This file type has a larger tooth Angle and is rougher than the ordinary metalworking file. This can greatly improve your productivity. Because the filed wax chip has a certain adhesion, so remember to clean your file often when using the wax file. This will remove the wax particles trapped between the file teeth.
Sandpaper is used to remove the marks left by various tools during the wax carving process so that the surface of the wax is smooth—sandpaper thickness model from coarse to fine from 220 mesh to 2000 mesh. Among them, I commonly use 400, 800, 1200.
Polishing technique
Polishing is the last process of wax carving production, and it is the method of smoothing the surface of the wax mold. The main methods I use are wiping and hot melt. In general, I recommend using the wipe method for polishing.
The wiping method uses the slight heat generated by the friction between silk and wax works to smooth the surface of the wax mold. Hot melt methods often use alcohol lamps and wax welding machines. You quickly move the piece back and forth over the flame, slightly melting the surface of the wax through the heat it emits. If you are new to wax carving, I do not recommend you use the hot melt method, because there are certain risks!